Establishing Industry Standards with Tailored Molding Processes
Tailored injection molding is a fabrication technique that has transformed the manufacturing of plastic components across multiple industries. By using this technique, manufacturers can manufacture intricate designs and configurations with remarkable accuracy and reliability. The process involves forcing liquid plastic into a casting, where it solidifies and solidifies to form the intended part. This ability has led to this approach becoming a preferred solution for businesses looking to manufacture premium components in large quantities.
Grasping the nuances of custom injection molding is crucial for companies aiming to set market benchmarks. With the potential to customize materials, designs, and fabrication techniques explicitly to meet particular requirements, businesses can attain enhanced efficiency and excellence. As a result, custom injection molding not only promotes advancement in product design but also improves competitiveness in the modern fluid market.
Comprehending Custom Injection Molding
Tailored injection forming serves as a manufacturing process employed to manufacture components by pumping molten material into a cast. Such a technique is particularly favored in diverse fields because of its efficiency and potential to create complex shapes with great accuracy. The process involves heating thermoplastic or curable materials until they become flexible, after that forcing them into sealed casts in which they solidify and harden into the the intended form.
One of the key benefits of tailored injection shaping is its ability to scale. After the original mold has been made, it can be used to manufacture thousands of identical components in a very brief duration. Such a renders it ideal for operations requiring high quantities of elements, such as automotive parts, household products, and medical instruments. The capability to reach strict limits and detailed designs makes certain that products fulfill stringent commercial standards.
Furthermore, custom injection molding provides significant material flexibility. Fabricators can choose from a range of substances, including synthetics, elastomers, and others, depending on the essential characteristics of the finished output. The ability to add supplements for color, strength, and additional characteristics allows for a high degree of tailoring, making this method an crucial solution for organizations aiming to retain competitive advantages in their markets.
Benefits of Tailored Solutions
Custom injection molding delivers a range of perks that greatly enhance production effectiveness and product quality. One of the main benefits is the ability to adapt designs to distinct client requirements. This adaptability allows businesses to create unique products that meet precise specifications, ultimately leading to greater customer contentment. Tailored solutions also facilitate the incorporation of novel features that may not be possible with conventional injection molded parts.
Another important benefit is the value of producing significant quantities of custom parts. While the upfront setup costs may be increased, the efficiency achieved during the mass production process frequently results in lower per-unit costs. Additionally, custom injection molding allows for the optimization of materials and processes, which can further reduce expenses and waste. This effectiveness is particularly favorable for industries that require large-scale production runs.
Moreover, custom injection molding offers enhanced design capabilities, enabling the use of cutting-edge materials and sophisticated geometries. With tailored solutions, companies can leverage advanced technology and high-performance materials that may not be available in ready-made products. This not only enhances product performance but also opens new opportunities for development and market separation, allowing businesses to stay relevant in dynamic industries.
Executing Best Practices
To attain optimal results in bespoke injection molding, companies should focus on careful planning and engineering of their molds. Engaging in a detailed design phase allows for changes that can reduce potential issues during production. This involves choosing the right materials and considering the flow characteristics and cooling times. Adopting computer-aided design (CAD) software can also enhance accuracy, leading to molds that effectively reduce waste and improve complete efficiency.
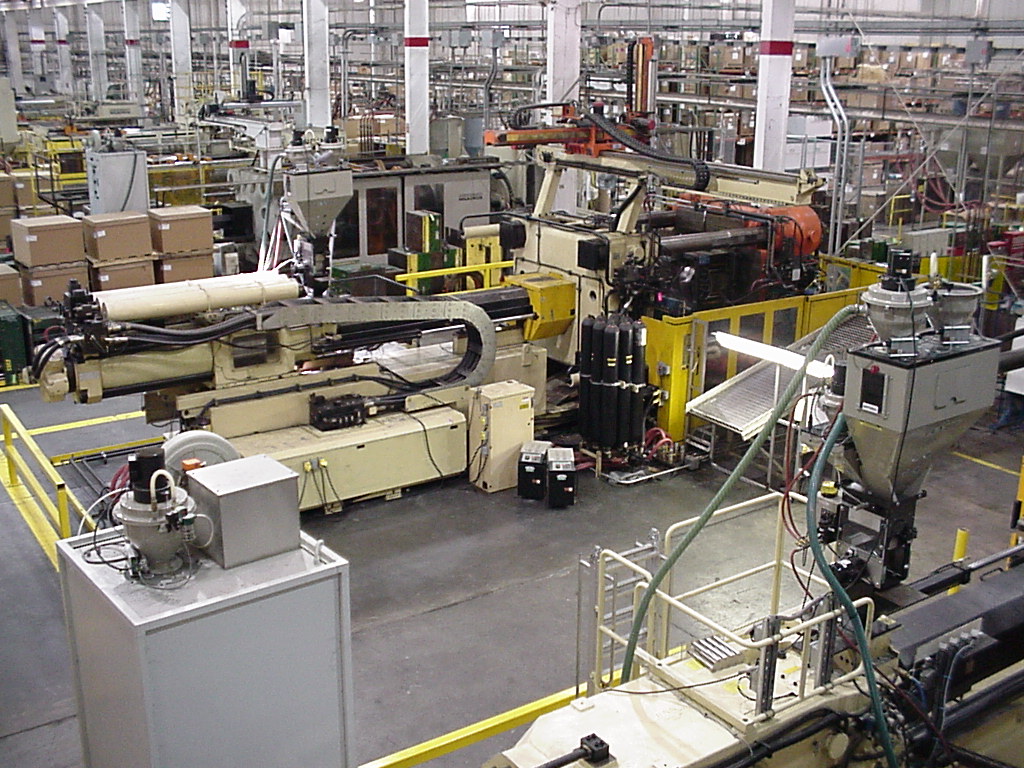
Another vital practice is to maintain clear dialogue among all stakeholders participating in the custom injection molding process. This includes cooperation between designers, engineers, and production teams to ensure that everyone is on the same page on project goals. Regular gatherings and updates can aid identify potential challenges ahead of time and foster a proactive approach in tackling them. Clear communication also applies to understanding client requirements, which ultimately leads to a better final product that meets particular needs.
Finally, continuous evaluation and refinement of the manufacturing process are crucial for staying competitive in custom injection molding. Implementing a feedback loop that reviews production data and identifies areas for enhancement allows companies to refine their practices over time. Investing in training and development for staff on the up-to-date technologies and methodologies also ensures that the team is equipped to adapt and innovate, driving superiority and efficiency in custom injection molding endeavors.